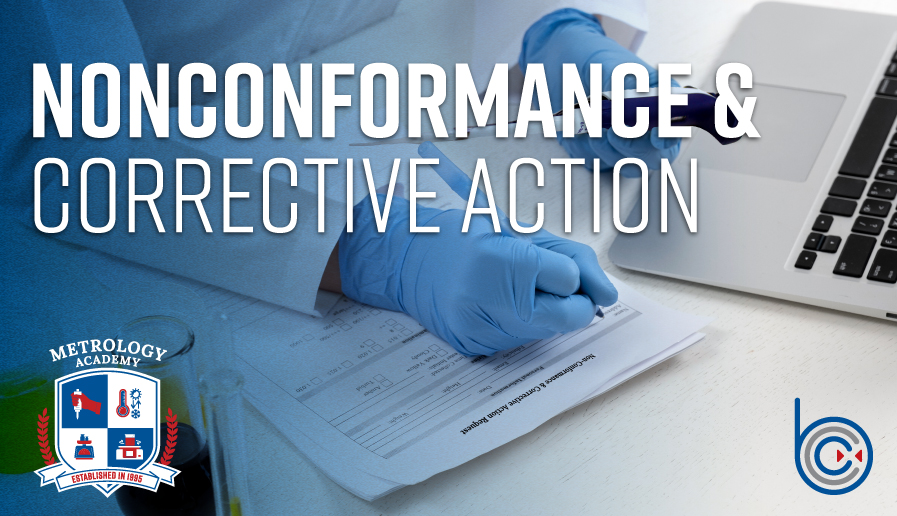
Nonconformance and Corrective Action
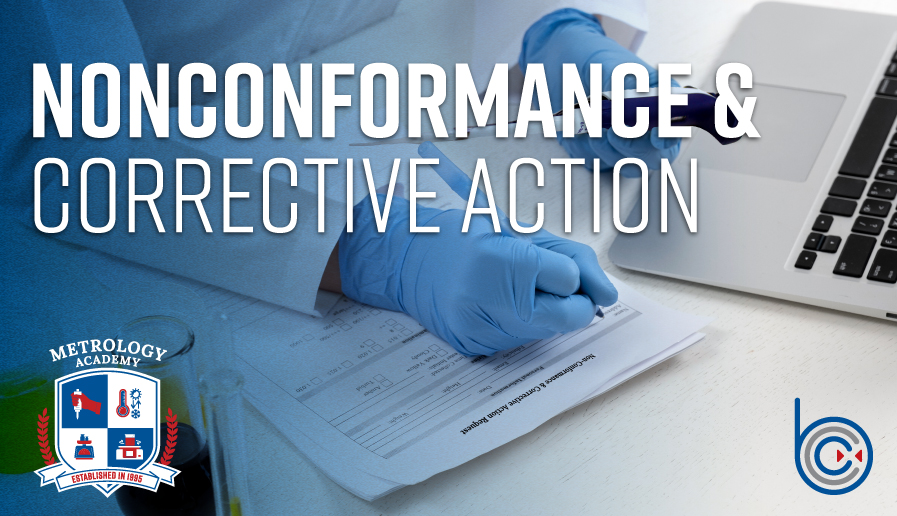
ISO/IEC 17025:2017 Accredited Labs are Required to Continuously Improve to Maximize Customer Outcomes
Many labs offer pipette calibration services. Knowing the quality of the services these labs will provide is essential. A lab should have a Quality Management System that focuses on continuous improvement. A Quality Management system with this focus will likely have some of these procedures in place: management review, internal audit procedures, proficiency testing, nonconformance and corrective actions, and other procedures that ensure necessary changes to the quality management system occur.
Working with an ISO/IEC 17025:2017 accredited lab is essential. When you choose to use an accredited lab to perform your pipette calibrations (like Bio Calibration Company), you are choosing a lab that is required to have these procedures in place. Not only do these labs need to have these procedures in place, but they are audited yearly by an accreditation company that ensures the lab meets the standard’s requirements.
Two of the required procedures from above were nonconformance and corrective actions. These are two critical procedures for a lab to have in place to promote continuous improvement and improve the quality of calibration services provided to its customers.
Nonconformance and Corrective Actions
Nonconformance is any work product that doesn’t conform to expected results, and corrective actions are initiated in response to nonconformances. ISO/IEC 17025:2017 accredited laboratories must identify and document nonconformances and determine if corrective action is needed to address them. Where corrective actions are ensued, ISO/IEC 17025:2017 requires several things regarding how the laboratory needs to document and carry out the corrective action. For example, a piece of equipment that continues to produce results out of tolerance could be a nonconformance. If the quality department deems it necessary, the metrology technician can initiate the corrective action and determine how to correct the problem causing nonconformance.
Examples of Reports
Here is an example of a nonconformance report and a corrective action report:
Let’s look at each aspect of this form and see why these components are so important. First is the “NCR/CAR number” field. The NCR/CAR field is integral to the nonconformance and/or corrective action procedure. It is simple, but using unique identification numbers for these forms allows for easy tracking of the form and its reference on other reports. For example, an Internal Audit Summary Report may need to reference any NCR/CAR reports initiated because of the audit. Having a way to track these NCRs and CARs with a unique identifier is important.
Second is the “Issue Raised by” field. It’s crucial to track NCRs and CARs and gather as much information from them as possible to help the lab continuously improve. So, having a record of each NCR and CAR and the source of where the issue was found will help labs identify which processes lead to improvement. For example, suppose you have 30 CARs initiated, and 20 of them were started because of an internal audit finding. In that case, your internal audit procedures are doing what they are supposed to be doing.
The Incident Description and Root Cause Analysis are the most crucial part of the NCR/CAR form. Describing the incident in detail is critical for clearly communicating the problem/nonconformance to others reviewing the form. Another reason the incident description is essential is because it provides enough detail for multiple people or departments to determine the root cause of the nonconformance. The root cause analysis is an integral part of corrective action procedures because it forces the collaborators on the CAR to investigate what caused the nonconformity rather than just document that it occurred.
The next part of the form is the Corrective Action field. This part of the process is obviously important. It occurs after the people assigned to the corrective action determine the root cause of the nonconformance. When the root cause is determined, the next step is for the appropriate or assigned persons to create an action plan to prevent future nonconformances. Typically, after a corrective action plan is proposed, the plan is forwarded to the Quality Assurance department. It is usually their responsibility to determine if the corrective action plan is sufficient and/or realistic to put in place.
What are some common challenges labs face when implementing Nonconformance and Corrective Actions?
Corrective Action procedures can often take time to complete. Each step is critical in making sure that similar nonconformances are prevented. One of the common challenges involved with corrective action procedures is not completing the corrective action in a timely manner due to a lack of resources. When labs are not strict about dealing with the corrective actions according to written procedure, sections often get overlooked. The root cause section is the most overlooked part of corrective action. Just because someone fills out the form with a best guess as to the root cause doesn’t mean it was done correctly. Determining the root cause of non-conformances sometimes takes more than just thinking about what went wrong. There are times when data collection is necessary to decide on probable root cause. This data collection can sometimes take planning and multiple departments to get done correctly. This is why root cause analysis is often overlooked: it takes resources to coordinate data collection and data analysis sessions. Sometimes, allocating these types of resources to solving specific problems is unrealistic. This is why having a good Quality Manager or Quality Department is so important. It should be up to the quality manager to determine how to fully allocate resources to complete corrective action reports.
Why are Nonconformance and Corrective Actions so Important?
Having procedures in place to address and correct non-conformances is important. The first and obvious reason is that the lab will have a way to identify and respond to nonconformances as they arise. The second reason is that these procedures promote continuous improvement of your laboratory and business processes. ISO/IEC 17025:2017 is a standard centered around a lab with a quality management system that supports continuous improvement. One critical aspect of that is the nonconformance and corrective action procedures. If the Quality department is in the habit of routinely writing non-conformances in the lab, that is a good thing. It’s good because the quality department can determine if corrective action is needed to resolve the regularly arising nonconformances. If non-conformances are not being written very often, the lab is running nearly perfectly, or the nonconformances are not being caught. Unfortunately, it’s usually the latter. So, having many nonconformances and corrective actions means that the quality department keeps a sharp eye on lab and business processes. It also means that interdepartmental communication is happening more often, which is always good.
How do you know if a laboratory has Nonconformance and Corrective action procedures in place?
The easiest way to tell if a laboratory has nonconformance and corrective action procedures in place is to check if they have an ISO/IEC 17025:2017 accreditation certificate. This standard requires the lab to meet the minimum requirements for responding to corrective actions. Here is what ISO/IEC 17025:2017 section 8.7 requires specifically. When a nonconformity occurs, the lab is required to:
If the lab you are outsourcing or considering outsourcing to is not ISO/IEC 17025:2017 accredited, it is still possible that they do have procedures to identify and correct nonconformances. Other standards require labs or businesses to have corrective action procedures. For example, ISO 9001 does require this. However, asking them for a copy is the best way to know if a lab has these nonconformance and corrective action procedures. These are usually documents that can be shared with potential customers. The records and corrective actions are not often shared with customers. Still, the policies and procedures governing these actions can be shared with customers and potential customers.
Conclusion
There are many choices for laboratories that offer pipette calibration services. Choosing the right provider is essential because the overall quality of the calibration services will significantly impact the customers. The best way to ensure you receive the highest quality calibration services is to see if they are ISO/IEC 17025:2017 accredited. Accredited laboratories must have quality management systems to improve their laboratory services continuously. Part of the requirements of those quality management systems is to have a way to identify and correct nonconformances that arise during the laboratory processes. These two procedures will ensure the customer receives high-quality calibration services.