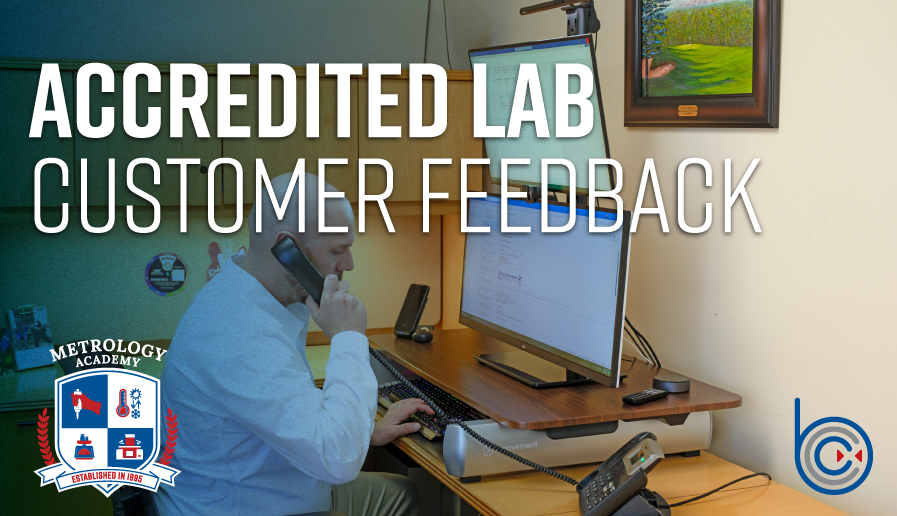
Improving Pipette Calibrations with Customer Feedback
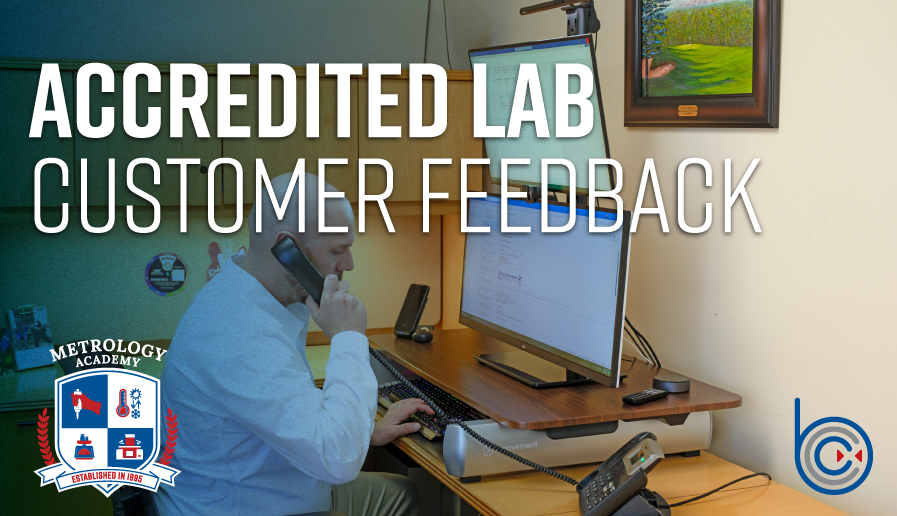
Outsourcing Pipette Calibrations to Labs that Use Customer Feedback
When choosing which lab to outsource your pipette calibrations to, it’s essential to consider whether they seek your feedback and use it to improve your experience. Labs that do this are usually more dedicated to providing consistent and reliable results because they want to improve their customers’ calibration experience continually.
A great way to instantly know if a laboratory has a procedure for getting customer feedback on calibrations and using that feedback to improve its processes is to check if the lab has an ISO/IEC 17025:2017 Accreditation. ISO/IEC 17025:2017 requires that labs seek customer feedback on their calibrations and use that feedback to improve their processes.
There are many other reasons why using ISO/IEC 17025:2017 accredited laboratories for outsourcing pipette calibrations is preferred. Read this blog post to learn more: https://biocalibrationcompany.com/blog/accredited-labs-for-calibration-services-versus-non-acrredited
What does an ISO/IEC 17025:2017 Accredited Lab do Differently Regarding Customer Feedback?
An ISO/IEC 17025:2017 accredited lab is required to seek customer feedback on the calibrations it performs, review this feedback, and use it to continually improve its procedures and processes.
The key difference between most non-accredited and accredited labs is the specific requirement that the customer feedback relates to calibrations and the results of calibrations. This is not to say that all non-accredited people improperly seek customer feedback or don’t do it at all. The point here is that ISO/IEC 17025:2017 accredited calibration labs are required to seek feedback and use it to improve their quality management system. All accredited calibration labs are required to do this, so outsourcing to accredited calibration labs means you are guaranteed that the lab will at least collect feedback. If you are outsourcing to a non-accredited lab, they may do this, but they are not required to do so.
Why is the Customer Feedback Requirement of ISO/IEC 17025:2017 Important to me as a Pipette Calibration Customer?
The reasons that the feedback requirement for accredited labs is relevant to calibration customers are:
Real-World Examples of Customer Feedback Improving Calibration Services
Suppose a biotech firm submits feedback to a calibration lab indicating inconsistent pipette turnaround times. An ISO/IEC 17025:2017 accredited lab must evaluate this concern through its corrective action procedures. The lab might analyze recent jobs, identify bottlenecks in their workflow, and implement new scheduling strategies to reduce delays. They may even use Key Performance Indicators (KPIs) to monitor whether these changes are effective.
Or a customer may notice a recurring issue where calibration certificates are being delivered with minor but inconvenient formatting errors, like incorrect serial numbers or units of measurement. Again, the accredited lab must document the issue, investigate the root cause, and update their certificate generation or review process. In both cases, customer feedback directly drives improved quality and consistency.
Accreditation Creates Accountability
Another benefit of the ISO/IEC 17025:2017 framework is its external oversight. Accreditation bodies conduct regular audits of labs to ensure they comply with all aspects of the standard, including how they manage and act on customer feedback. These audits hold the lab accountable and validate that improvements are being implemented as claimed.
This type of accountability creates a culture of transparency and customer focus. Knowing that an external body monitors the lab’s performance can reassure customers that their interests are protected. It also motivates labs to stay proactive and diligent in their quality management efforts.
How to Maximize the Value of Your Calibration Relationship
As a customer, you can also actively ensure your feedback is heard and applied. Here are a few ways to get the most value from your relationship with an accredited calibration lab:
Building a strong, collaborative relationship with your lab fosters mutual trust and accountability. Over time, this leads to more reliable calibrations and smoother experience overall.
Customer Feedback isn’t just a Bonus, a Requirement in ISO/IEC 17025:2017 Labs
In the world of pipette calibration, accuracy, consistency, and accountability are non-negotiable. ISO/IEC 17025:2017 accredited labs offer these benefits not just because they claim to, but because they are required to by a rigorous international standard. A key part of that requirement is actively seeking customer feedback and using it to drive improvement.
Accredited labs’ commitment to evolving alongside their customers’ needs sets them apart. For calibration customers, this means peace of mind. It means knowing your feedback won’t vanish into a void but will be part of a larger quality assurance system and continual improvement.
Outsourcing to an ISO/IEC 17025:2017 accredited lab ensures that your voice is not only heard but built into the very foundation of the lab’s operation. And when it comes to critical tools like pipettes, that kind of commitment to quality isn’t just nice to have—it’s essential.
Real-World Examples of Customer Feedback Improving Calibration Services
These real examples show how ISO/IEC 17025:2017 standards create mechanisms for feedback to translate into visible, measurable service enhancements.